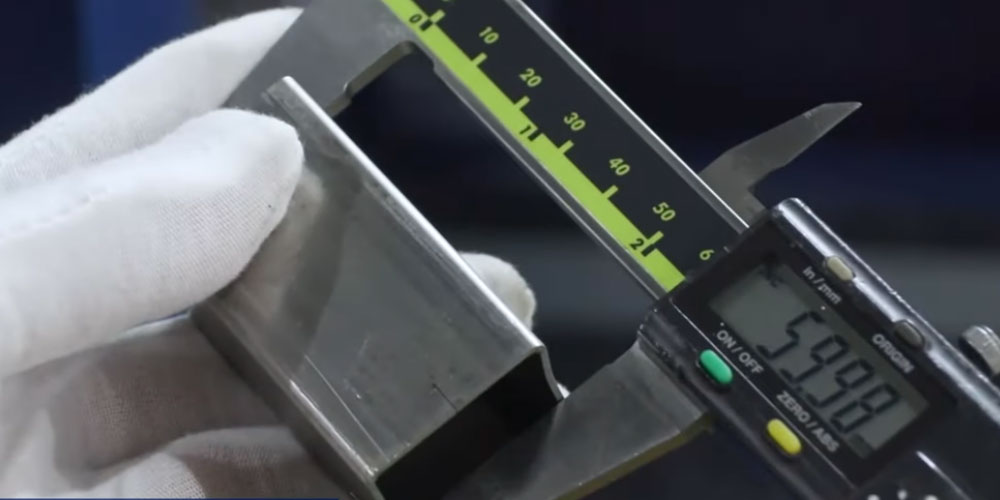
by Eric St. James
Published at 2020-05-14
Preventative maintenance is a core activity for any shop, big or small. No matter the number of machines or volume of work, proper upkeep is crucial to running a metal fabrication business. One powerful preventative maintenance factor is a regular machine inspection.
Regardless of shop size, scheduling annual inspections with qualified technicians yields high ROI. It could save your business in three critical ways:
Here are some of the benefits of regular machine inspections:
There’s no limit of what you could find in a detailed inspection. The goal is to identify any potential issues before equipment failure. Catching any problems before a complete breakdown happens can be significantly less expensive to fix. It could be as simple as pointing out an incorrect or insufficient maintenance procedure.
There’s never a good time for machines to fail. You’ll be thankful you caught it in advance so you can plan to fix the issue in the most time and cost-effective way for your business.
Even the most detailed machine inspections will only take a couple of hours. That limited amount of downtime could end up saving you much more down the road.
This is especially true for smaller shops that only have one machine. You’ll want to stay on top of inspections or risk being completely shut down. Likewise, for any upcoming big jobs; you want to ensure your machines won’t let you down halfway through.
Typical machine inspections are relatively inexpensive. It’s a small price to pay for something that could save you big in the future in terms of future maintenance, fixing any issues, and potential downtime.
A good inspector will be quick and thorough. Any issues that are found might end up costing you, but catching it early will likely be far less expensive.
Timing is important
For most equipment, you’ll want to plan on detailed inspections at least yearly. The good news is you can schedule multiple routine maintenance activities together to further limit your downtime. For example, you could couple your machine inspection with oil changes.
Learn more:
· The importance of regular oil changes for your equipment.
· Avoid unplanned machine downtime with preventative maintenance.
Experience is critical
When considering suppliers for machine tool inspections, you’ll want to be confident with their level of knowledge and experience. There is no point scheduling an inspection if the technician performing it doesn’t know where or what to look for.
At Paramount Machinery, with our decades of experience in metal fabrication machinery service and inspection, we know not everything is surface level. You need to know how to look under the covers and why.
One classic example of a critical item that could fail is an under-appreciated coupling. This component joins an electric motor to a pump and is typically hidden deep in the belly of the machine. You would never see or think to look at it, but if this piece fails, it will cause a complete machine shutdown. The only time you’d find out if there is an issue, is with an inspection performed by a qualified technician that knows to strip everything else away to see it.
Over the years, we have created our own checklists by machine type and model – and are continually assessing and expanding them – to ensure we are thorough and efficient.
Keep your machines healthy and your bottom line strong
Like your annual visit to the doctor for a physical, routine machine inspections are relatively painless activities that reap great rewards, including catching potential problems early. Once you get a clean bill of health, you can confidently continue running your machines and fulfilling jobs to keep your customers happy, and your bottom line strong.
{{cta('601f05f0-3914-4a8f-87e4-902eb851fa8c')}}
© 2023 Paramount Machinery Inc. All rights reserved.