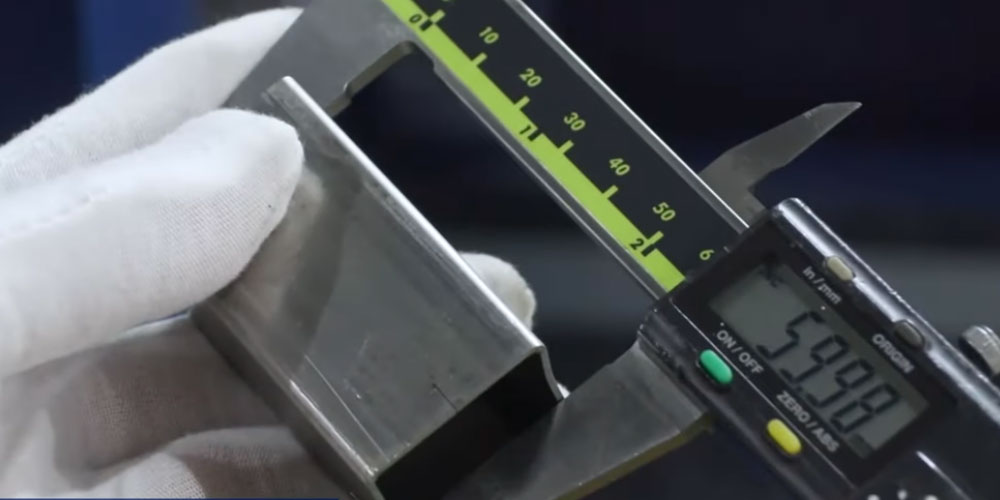
by Eric St. James
Published at 2020-05-27
For the past few years, fiber lasers have been the talk of the metal fabrication industry. It can be easy to get caught up in what’s new and powerful, but let’s not forget about a common technology that has been getting the job done for decades: Plasma Cutting Systems.
Thousands of plasma tables can be spotted across North America. Dating back as far as the 1960s and developed for cutting sheet metal in the 1980s, this technology has evolved and is an effective complement to fiber lasers and other cutting equipment.
Plasma Cutting uses an accelerated jet of hot plasma to cut through electrically conductive metals.
Here’s how it works:
When it comes to cutting sheet metal, there are multiple equipment options to consider. Depending on your product mix, a plasma cutting machine can be an excellent addition to your shop floor.
Here are our top benefits to choosing a plasma cutting machine:
One top advantage to plasma cutting technology, is that the electric arc process can cut virtually any electrically conductive material.
While plasma cutting machines may not be as fast as other options, their strengths lie in cutting thicker materials in lower volumes. Typically, you’ll see plasma cutting excel with materials like steel ¾” and thicker.
The biggest advantage of plasma cutting technology is the cost factor. This technology has advanced significantly since entering the market, allowing fabricators to effectively cut a multitude of materials for a much smaller initial investment.
Plasma cutting machines can be a fraction of the price of a fiber laser. While operating costs tend to be comparable to fiber lasers, you can’t beat the savings in initial upfront costs for plasma equipment.
Plasma cutting technology is relatively accessible and effective, for a variety of applications. It’s no wonder it has gained widespread use from large-scale industrial fabrication to smaller hobbyist shops.
© 2023 Paramount Machinery Inc. All rights reserved.