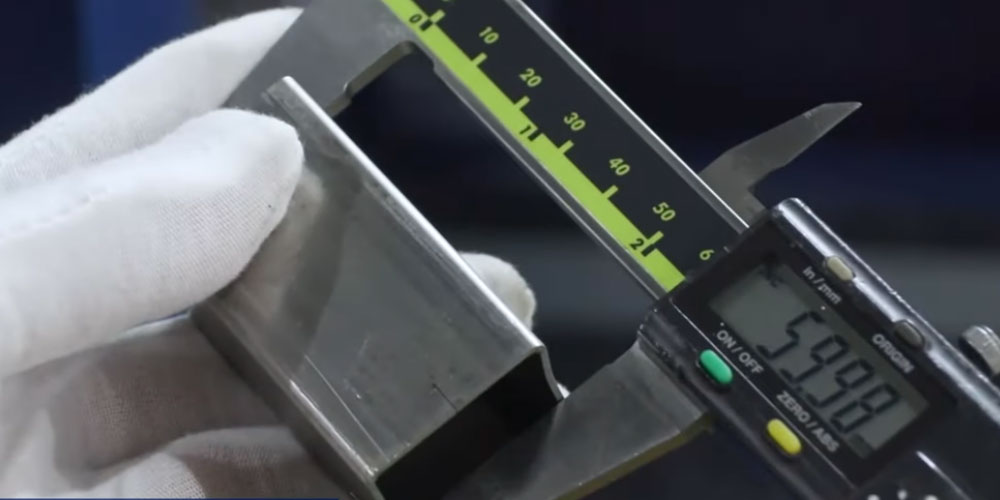
by Eric St. James
Published at 2023-10-04
Your current CAD/CAM software is likely capable of managing many cutting technologies and is an automated and effective productivity solution. Nesting is a standard function most often identified with maximizing material utilization in flat sheet material, but is also available for tube cutting to enable the same increases in efficiency. Similar to flat material, nesting for tubes is used to set up optimal part distribution, maximum material use, and aids in the production planning process by calculating the material needed to produce the required parts.
Jobs involving cutting tubes for a specific project can require many different lengths and profiles of the same tube size in various quantities. Tube nesting takes these different parts and finds the best way to arrange them in the predetermined lengths of raw tube with a view to maximizing material utilization while calculating the total number of lengths required. Often, multiple configurations are available thereby permitting Production to plan accordingly and to pick the best outcome for the shop. Production planning now has the data to determine anticipated production time and what material to order.
In order to get optimal material usage with the best part distribution, and to reduce the most amount of waste, nesting software can predetermine the material occupancy of a production batch on tubes of different lengths. You can then set up and run nesting to account for different quantities of tubes or sections of different lengths. This can include utilizing pieces from previous jobs thereby further reducing waste in your shop and saving you money.
Tube nesting software improves your laser tube cutting efficiencies. Your fabrication shop will enjoy higher productivity, optimal material usage and maximum reduction of waste, resulting in lowered production costs and a high return on investment.
© 2023 Paramount Machinery Inc. All rights reserved.