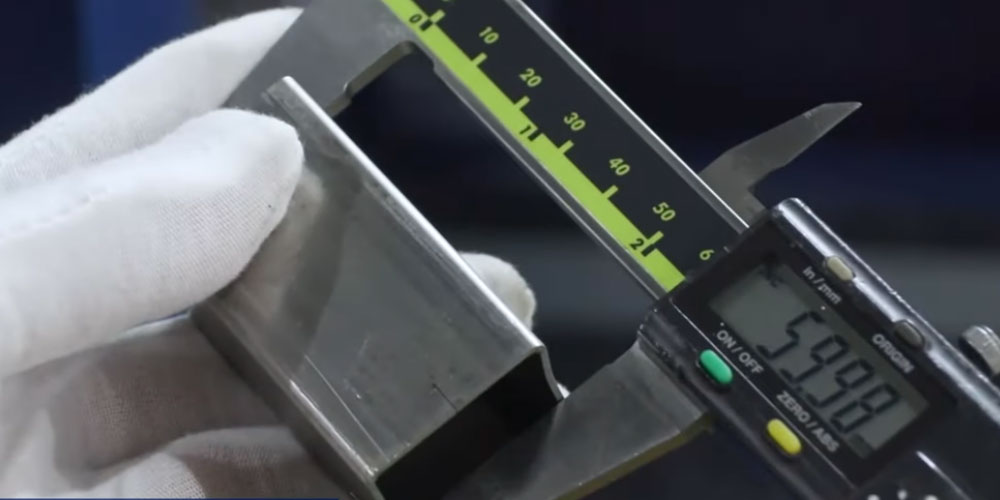
by Eric St. James
Published at 2021-11-30
Assist gas is essential for all laser cutting processes. Its core job is to blow molten metal away from the beam kerf. This is necessary for all types of metals. The most popular assist gases are nitrogen and oxygen. There is also a third option: high-quality compressed air.
Compressed air has been growing in popularity over the past couple of decades and is quickly becoming one of the top assist gas choices for laser cutting. There are three main reasons for this: Quality, convenience, and cost.
Since air is a blend of mostly nitrogen (78%), oxygen (21% and argon (0.9%), using compressed air as an assist gas is very similar to cutting with nitrogen. You can expect to reach cut speeds comparable to nitrogen and the result is a high-quality cut for many materials – particularly for thinner metals. Compressed air is especially effective in aluminum cutting, for example.
There is no question that convenience is a major factor in deciding to cut with compressed air. Similar to on-site nitrogen gas generation, when you switch to compressed air and invest in a high-pressure compressor and filtration system, assist gas costs begin to drop substantially. No need for tanks, refills, or delivery concerns. This is especially beneficial during the pandemic, where global supply chain disruptions have led to shortages of oxygen and nitrogen in many regions.
Cost is one of the top reasons fabricators are switching to compressed air. Since fiber lasers started gaining ground in the industry, we saw gas consumption increase significantly. People started looking at alternatives to keep costs down, while keeping quality and productivity up. This all makes compressed air a great option. Not only is it an excellent assist gas, but it is also cost effective. You can make a one-time investment in equipment to generate the proper compressed air quality on-site and enjoy a very low-cost assist gas supply. Many fabricators see returns on investment in less than two years.
When you consider the abundance and convenience of compressed air, comparable quality to using nitrogen, cost-saving benefits, plus the fact that many machines like the Eagle Fiber Laser come with the standard feature to switch from traditional assist gas to compressed air – it’s a no-brainer for many fabricators.
{{cta('601f05f0-3914-4a8f-87e4-902eb851fa8c')}}
© 2023 Paramount Machinery Inc. All rights reserved.