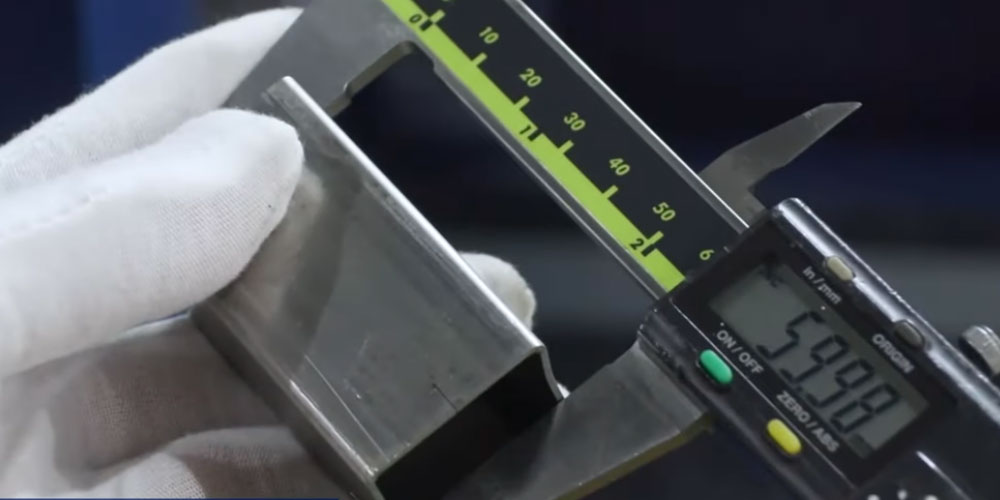
by Eric St. James
Published at 2014-11-07
Many fabrication shops operate very well with machinery that is not new. It’s not uncommon to find various types of equipment that could be 20-30-plus years old and functioning very well for the company.
However, when an unplanned machine breakdown occurs managers may find themselves discovering that their machinery, or parts thereof, could actually be obsolete. It’s not until calling around for a replacement part or attempting to upgrade that problems are encountered.
Other than the obvious repair challenges, utilizing obsolete equipment can cause quality issues, slower processing speeds, and actual breakdowns or failure, which can result in severe downtime and the unforeseen associated costs for your fabrication shop.
When facing a breakdown or failure on your production line, a manager’s first response is often to contact the original equipment supplier. Unfortunately, they may not be able to provide solutions to your crisis.
You may be faced with issues such as:
Well-maintained, regularly serviced and upgraded equipment - even machinery that has a couple of decades of use under its belt - usually results in good production quality.
Still, there can be circumstances where there’s a problem on your line, and it’s only then that you will find out if your equipment can be easily serviced or replacement part can be found and installed.
Although there are many obvious benefits of upgrading/replacing parts and, where necessary, buying new or previously owned fabrication machinery, many fabrication shops are hesitant to do so.
Generally, a good rule to keep in mind is: when you can no longer get the parts you need, or the service expertise for a piece of equipment, it has become a liability to your business. In other cases the costs of replacement parts may be prohibitive if your machine is quite a bit older. As the equipment’s market-value dwindles, the justification to repair the machine becomes impossible.
Upgrading or replacing equipment in your fabrication shop may not incur such significant costs as may be expected.
Increase productivity in your shop by upgrading machinery, replacing parts or key components, or replacing entire machines with new or previously owned equipment. This will result in a good ROI over the long term and can help your company’s bottom line.
{{cta('fb4aa075-2f36-4b88-8a5e-87408785c274')}}
© 2023 Paramount Machinery Inc. All rights reserved.