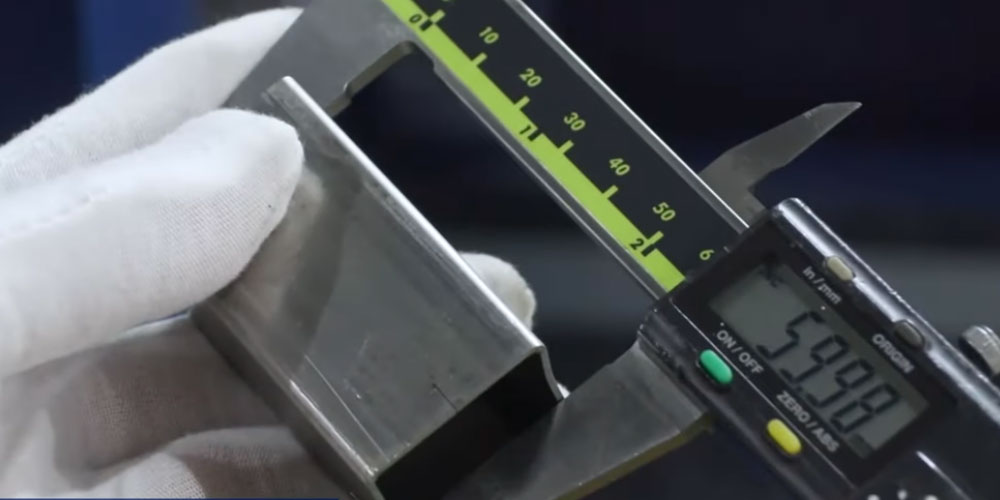
by Eric St. James
Published at 2021-04-14
As people around the world become increasingly concerned about pollution, the environmental impact of manufacturing cannot be ignored. Like many industrial processes, metal fabrication comes with ecological and workplace health concerns that vary by process.
All metal cutting methods generate residual products. From laser and plasma machines to water-jets, each process produces different types of waste at varying levels. Fortunately, there are ways to mitigate waste and pollution.
When it comes to energy saving, fiber lasers get top points. Energy efficiency is one of the top benefits of the technology, allowing you to save on operating costs. Beyond power consumption considerations, all laser machines produce vaporized smoke and metal. This bi-product of laser cutting is a high-risk pollutant, requiring a strong ventilation system to protect your crew and the outdoors where the system is ultimately exhausting.
Your dust collector should be properly sized and maintained for the application. It is also important to ensure monthly inspection of the filter cartridges. This applies to both laser and plasma machines.
This thermal metal-cutting process creates a large amount of smoke and metallic dust with serious health implications. Mitigation for pollution risks include proper ventilation and dust and fume collection systems similar to lasers.
In response to this issue, manufacturers like Komatsu have introduced a new concept to their plasma machines. External fans in the machine frame “pressurize” the cutting area drawing smoke towards the exhaust ports. This ensures maximum efficiency of the down-draft effect created by the exhaust ports located under the cutting area resulting in significantly cleaner work environments.
The waterjet cutting method is one of the greener processes in the industry.
There is no metal burning, so waterjets don’t create fumes or air pollution. Plus, they don’t require cooling or lubricating oils, and the water and garnet abrasive used to cut metal have worldwide availability and require minimal pre-processing.
The environmental consideration to keep in mind with these machines revolves around garnet removal. While smoke and metallic dust are both concerns of plasma and laser processes, they don’t require waste disposal in the same capacity as waterjet machines.
Because the sand abrasive used to cut metal becomes contaminated, it must be removed as a waste product. Most often, this waste is not hazardous and is generally accepted at landfills without concerns about environmental risk.
For fabricators in some regions, there is another option – waterjet abrasive recycling. While not widely embraced, there is a garnet recycling market. Some shops have implemented recycling equipment, but capital and operating costs are some of the reasons this practice hasn’t caught on. For those that aren’t up for bringing on their own recycling program, businesses like Garnet Recyclers of Washington are working hard to improve the garnet recycling model.
As the technology and market evolves, there may be increased support for recycling garnet, particularly when considering the opportunity to cut commodity costs. We encourage you to investigate garnet recycling options in your area.
As more businesses are becoming increasingly eco-conscious, we can’t ignore our footprint in the manufacturing sector. While the bulk of the decision-making for machine tools will be based on application, there is room for consideration of the environmental impact and mitigation in every shop.
{{cta('601f05f0-3914-4a8f-87e4-902eb851fa8c')}}
© 2023 Paramount Machinery Inc. All rights reserved.