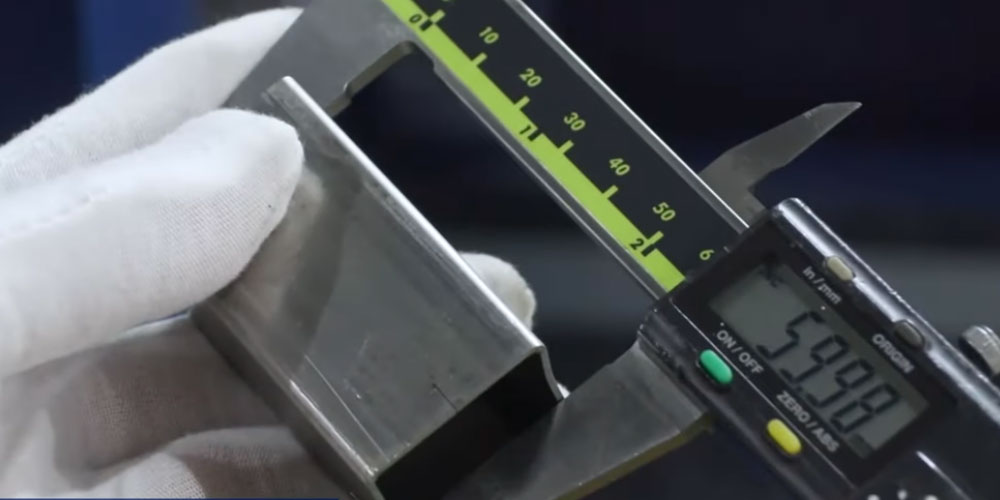
by Eric St. James
Published at 2020-07-24
In metal fabrication, all laser machines – including C02 and fiber lasers – use some sort of assist gas in the cutting process. It is an essential component of laser cutting and can account for 60% of the operating cost. While there are other options, nitrogen is the most commonly used assist gas.
For such a significant player in day-to-day laser cutting operations, what is nitrogen’s role and how can fabricators reduce supply costs?
Nitrogen is the most popular industrial gas used throughout the industry and plays a crucial role in laser-cutting of metals.
Nitrogen has two applications in laser-cutting processes:
· as an assist gas to help prevent oxidation
· as a purging gas in C02 machines
The main benefit of using nitrogen as an assist gas is to prevent material oxidation. This results in a higher-quality finish and helps reduce preparation time for secondary operations like welding and painting.
Oxidation occurs when oxygen mixes with ambient moisture to create corrosion. Pressurized nitrogen displaces oxygen in the cut path while reducing heat. Oxidation can affect the surface appearance of the finished product but also affects the cut edge. Nitrogen is also used to produce a clean edge, reducing residual material (also known as dross) by constantly clearing the kerf of molten material as the beam progresses through the cut.
Nitrogen is also used for laser beam purging in C02 machines. In all laser cutting processes, a clean laser beam stream is necessary to prevent irregularities and ensure productivity. While purging the path is not required for fiber lasers, it is critical for C02 machines as they use lenses and mirrors to focus and reflect the laser beam as it travels to the head.
Nitrogen helps prevent contamination of the beam by purging the beam “path” and pushing out moisture, CO2, and other contaminants that would affect the laser. It also helps keep lenses and water-cooled mirrors free of dirt, water vapour, and more. Industrial nitrogen is an ideal purging gas because of its inherent cleanliness and purity.
The main advantages of using nitrogen for laser cutting machines are:
· Reduced oxidation
· Clean cut edges
· Dross-free finish
· Productivity enhancement
Nitrogen is an essential consumable that must be backed up by a reliable source There are basically two options for obtaining nitrogen:
· Outsourced supply
· Nitrogen generating systems
The traditional method of obtaining nitrogen gas is by using a third-party supplier. This method can account for up to 60% of your operating costs.
Depending on your needs, it can get very expensive. You’ll also want to ensure your supplier is reliable and consider delivery, storage, and space concerns. Bulk-packs of 16 cylinders provide some discount, but storage and material handling become issues. Bulk-buying nitrogen can be a more cost-effective route, however provisions must be made to accommodate a large storage tank outside. Furthermore, good quality piping must be installed to deliver the gas to the laser machine.
Outsourcing supply also comes with certain challenges like potential price volatility, taxes, environmental fees, health and safety issues, and delivery constraints.
Nitrogen generators are a great option, especially for fiber lasers that typically require higher consumption. On-site nitrogen generation systems allow you to produce all the nitrogen you need, when you need it. In addition to controlling your gas supply, this option comes at a fraction of the cost compared to that of an outsourced supplier.
Investing in a nitrogen generator is one of the top ways to cut laser operating costs and improve operational efficiency.
{{cta('849fa231-0b41-4ba1-abb3-6a1718e8c43f')}}
© 2023 Paramount Machinery Inc. All rights reserved.