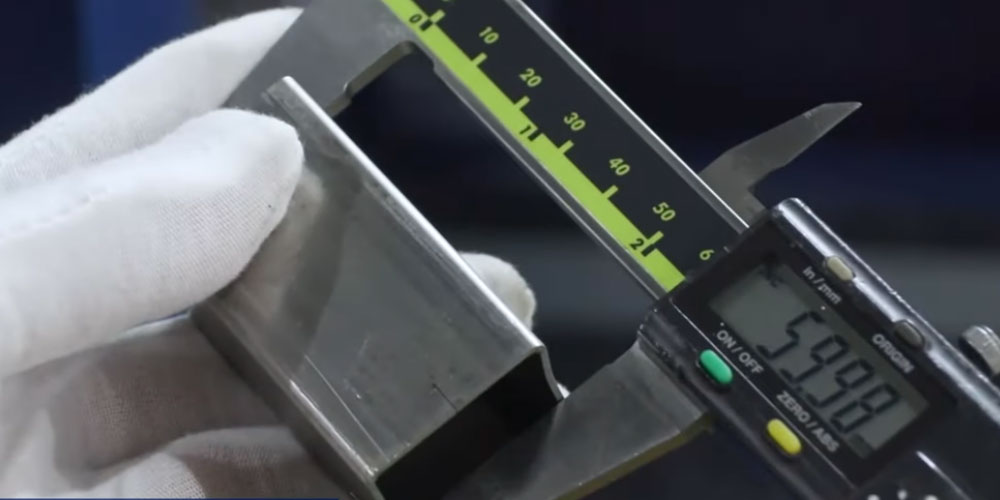
by Eric St. James
Published at 2016-10-13
Compressed air circuits are an integral component of most machine tools. The quality of the compressed air is even more essential. Here’s why it’s important for productivity and how to ensure the compressed air being distributed through your machine tool is in the best state for top results.
Compressed air drives many different machine functions including work clamping, position cylinders, shot pins for turret location, and indexable station drives to name a few. While these features may have different uses they all have common elements: a solenoid valve and an actuator. Both of these components need clean and dry air and in most cases the air must also be lubricated. Low quality air, including air holding moisture and impurities, can cause rust and reliability issues – all impacting productivity.
The quality of the air is critically important to the reliability of your fabrication machines and ultimately your fabrication shop. This is why the source and delivery of your compressed air must ensure it is clean, dry, and lubricated before it gets to the machine.
While we can’t see impurities in the air it often doesn’t reach our machines in the best condition. Air delivery systems aren’t perfect! Since air lines tend to be the same pipes that deliver air to the entire factory floor the air picks up debris and condensed water along the way arriving at the machine in less than pristine condition. As the air picks up impurities throughout the process it needs to be filtered before it reaches the machine.
The FRL performs all three functions for compressed air: it filters, regulates and lubricates. While this device is critical it is often overlooked. For many machine tools it is the only line of defence between poor quality compressed air and your machine’s pneumatic circuit. This component prepares your compressed air so you can be sure your machines are receiving top quality energy.
While it can vary depending on machine, for most, the FRL supplied by the equipment OEM is only meant to prepare air in the final stage of the process. The filter portion of the FRL is usually quite fine with a small capacity. It isn’t always able to filter out large quantities of water and debris and can get contaminated quickly. Many fabricators using the FRL as the sole compressed air preparation component assume the air is fairly clean to begin with.
If your compressed air system is not equipped with a dryer it is a good idea to install a large capacity water separator and filter in the air line to your machine before it reaches the FRL. Compressed air gets hot – this leads to water condensing in it. As refrigerated units, dryers cool the air and remove moisture and are equipped with a filter. In short a good dryer ensures good, clean, and dry air arriving at the machine.
If you don’t have one, don’t sweat it, not everyone does. However, you will need a primary filtration unit to act as a pre-filter before the air reaches the FRL.
As with any feature of machine tools, regular maintenance is key to performance and productivity for all metal shops. Following a maintenance schedule can prevent any issues that could slow or halt production and cost you money in repairs. Specifically proper maintenance on the pneumatic circuit can prevent downtime and premature solenoid and actuator wear. Cylinders and valves risk seizing up if they get too dry.
Your compressed air maintenance checklist:
Your lasers, press brakes, punch presses and other machines are the heart of your fabrication business. It’s in your best interest to set them up for success. Starting with quality compressed air is the first step!
{{cta('0b48f020-786b-442e-98c2-be413edc27ea')}}
© 2023 Paramount Machinery Inc. All rights reserved.