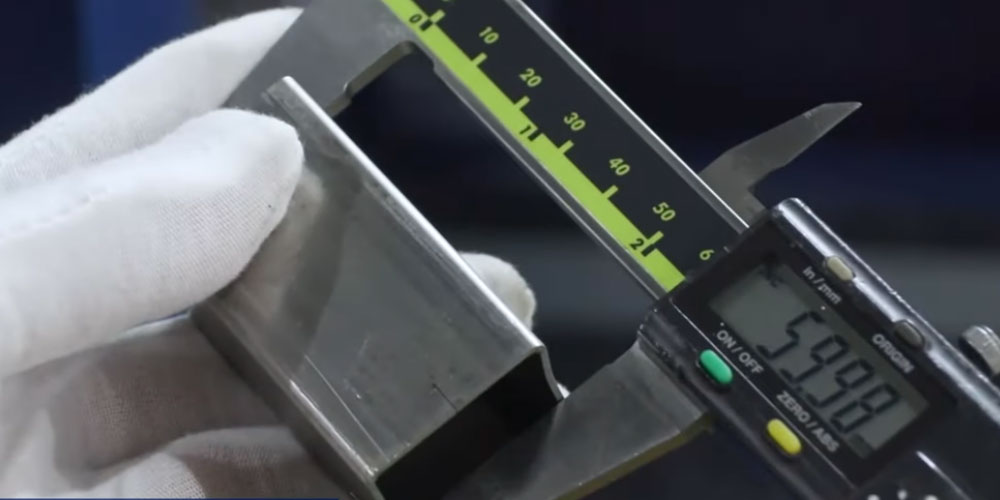
by Eric St. James
Published at 2022-01-13
Global supply chains have been a defining news topic in 2020 and 2021. We are facing shortages of raw materials around the world. Manufacturers struggle to keep up with unexpected demand as economies begin to bounce back from the pandemic, worker shortages plague plants and warehouses across North America, costs continue to rise, and worldwide shipping delays are holding us all back.
Almost all sectors are confronting supply chain disruptions this year. Manufacturing has seen some of the highest delays – with steel, lumber, and other raw material shortages causing industries like the construction and motor vehicle sectors to bear the brunt of it. Why? The COVID-19 pandemic was a key player in the supply chain crisis, but unexpected events and natural disasters – like a deep freeze in Texas and the blockage of the Suez Canal – also played a role.
What are we facing in the metal fabrication industry? The most significant challenge we’re seeing is the supply delays and astronomical price increases for steel. We haven’t seen it ease up yet. Back in May we were struck by the cost of hot-rolled coil steel rising to a record high of USD$1,540 a ton, tripling the 20-year average. By September, it continued to climb to a peak of USD$1,955 a ton. The cost of steel was top of mind for fabricators this year, and we expect to continue hearing about it in 2022.
While the just-in-time manufacturing mantra has worked to allow companies to adapt to market demand and avoid waste and excess inventory, this needs to be reconsidered given today’s reality. Reactivity is a way of the past, given how unprepared many companies were for the disruption and demand we faced this year. We’re now forced to think about how our production models reflect current and future risks.
Now is the time to consider where and how you’re getting your materials and supplies. Many companies are updating their relationships with supply chain partners and expanding their strategy. We’re seeing businesses prepare for vulnerabilities by opening factories in multiple locations, investing in warehouse footprints and logistics, as well as diversifying vendor partners and nurturing those relationships so they don’t get caught in a snag.
Others are even making the move to vertical integration for more control over their supply chain. We’re specifically seeing this in the automotive industry, where manufacturers are moving responsibility for core components in-house instead of using external vendors.
One thing we can’t deny is that the world is changing fast. If we can’t evolve with it, we’ll be left behind. That’s why it’s so important to adapt, adjust, and embrace technological advancements to get ahead of the curve.
For example, automakers like Nissan and General Motors are adapting to overcome challenges caused by the shortage of semiconductor chips. Nissan is said to be redesigning its cars to use more generic chips for certain functions. This will allow a reduced reliance on custom-made chips and avoid risk of production delays. General Motors is also pivoting, by looking to co-develop semiconductors for multiple tasks in its vehicles. This will simplify the variety of chips it uses to just three product families, again helping to reduce risk.
In metal fabrication, there are incredible new technologies that can allow you to reduce risk and adapt to the changing markets. For example, new CAM software can help bolster material and machine efficiency. Advancements in machinery like High powered fiber lasers are another good example. When demand is up, you’ll appreciate how increased power and speeds can boost production capacity and bump up parts per hour. When worker shortages are a concern, you’ll love how the latest fabrication technology can help consolidate your operations and save on labour.
During 2020 and 2021, the COVID-19 pandemic forced us to rethink supply chains and how we operate in manufacturing. Can we take all the challenges presented by global supply chain disruptions and transform that frustration into opportunity and create a better future for the manufacturing and metal fabrication industries? We think fabricators and the industry in general will continue to adapt and improve as they always have. What choice is there after all?
{{cta('601f05f0-3914-4a8f-87e4-902eb851fa8c')}}
© 2023 Paramount Machinery Inc. All rights reserved.