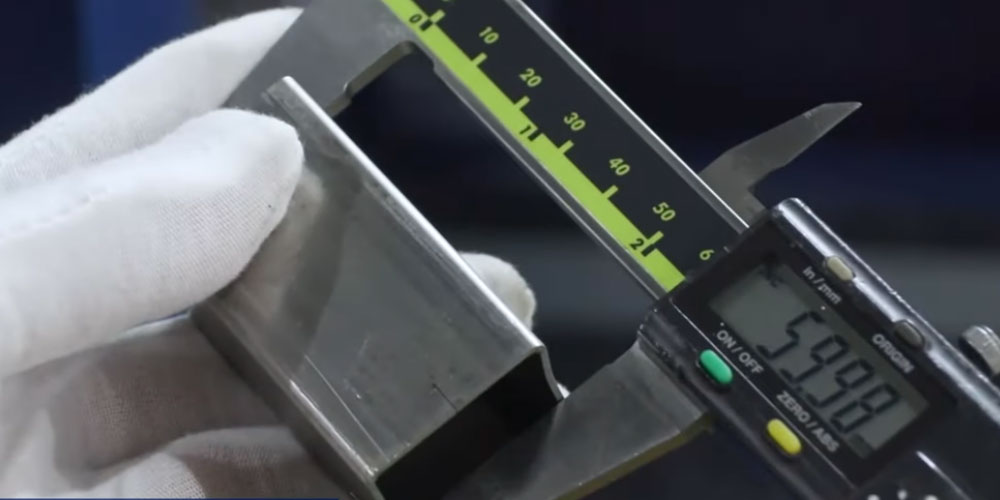
by Eric St. James
Published at 2014-03-13
Cutting processes
Metal fabrication companies today are looking for more than just speed in their operations. They require equipment that adds capabilities and flexibility. New machine technology permits manufacturers to offer more services to their existing customers, bring in new customers, and boost overall productivity.
The two cutting processes most often used by metal fabricators are waterjet and laser cutting. How do you determine which one is best for you?
Questions to consider
What material are you cutting? What is the thickness of the material? How much accuracy is necessary for the job?
Both waterjet and laser cutting machines have many useful features, benefits and advantages. Manufacturers are cutting metal, stone, plastic, acrylic, and even food, and laser and waterjet technology are making these challenges routine.
What’s involved in waterjet and laser cutting?
Waterjet cutting utilizes an extremely high pressure stream of water, usually between 60,000 - 90,000 PSI, typically with an abrasive substance, such as garnet, injected into the stream. The water is effectively a delivery medium for the garnet that actually does the cutting.
No heat is used or generated during waterjet cutting. Since there is no heat affected zone (HAZ) the risk of material distortion is greatly reduced making waterjet-cutting - along with routing - a preferred solution for the aerospace industry.
Laser cutting utilizes high-powered (1,500 - 7,000 watts) lasers with specialized lenses and mirrors, to produce a focused pinpoint beam of light, from .005” to .010” in diameter. The laser melts the material and a high pressure jet of “assist” gas blows away the molten material. Assist gases are typically nitrogen or oxygen.
What are you cutting?
While most industries still require basic metal-cutting services, some companies are utilizing newer applications in their operations. Fabricators often report increasing requests to cut a wider variety of materials than ever before including exotic metals and composite materials. Both waterjet and laser equipment can be used when cutting many different types of materials.
Material thickness
Lasers are well-suited to cutting metals under 1” in thickness. Waterjets can easily cut almost any material and can cut thicknesses in excess of 12”.
Degree of accuracy your job requires
Both waterjet and lasers are proficient in terms of accuracy. When determining which application is best suited for a particular job, part features must be considered (i.e. small holes, material hardening, required flatness, etc.).
Waterjet cutting capabilities include tolerances as close as +/-.003”, and laser cutting capabilities include tolerances as close as +/-.002”.
Speed
Lasers often have a speed advantage over waterjets. For example, on 1” thick carbon steel, a waterjet with a pump that delivers 60,000 psi, equipped with a 0.014” orifice and a 0.030” nozzle, consuming abrasive at a rate of 1.2 pounds per minute, cuts at 75 mm/min. A 3,800 watt laser, equipped with a 2 mm coaxial nozzle, and using oxygen as the assist gas at 8.4 PSI, can cut more than eight times faster at 622 mm/min.
However, a waterjet machine can cut through much thicker metals, as well as many other types of materials, with great ease. Some more exotic examples include 150mm thick aluminum, 450mm stainless steel, and 350mm stone.
It’s important to note that newer, higher-pressure waterjet machines have been developed which can considerably speed up the cutting process. Cutting speeds in 70mm steel with 60K PSI are in the vicinity of 10~14mm/min. Cutting speeds in the same material with 90K PSI are over 30mm/min.
Benefits for your machine shop
Both laser and waterjet machines have good life expectancies as they don't use dynamic machining forces and aren’t in contact with the workpiece during the cutting process. Either cutting machine can get a job done well for your machine shop with relatively low setup costs, since fixed tooling and fixturing are not usually required.
Fabricators should keep in mind the material to be cut and the requirements of the job at hand when making purchase decisions.
© 2023 Paramount Machinery Inc. All rights reserved.