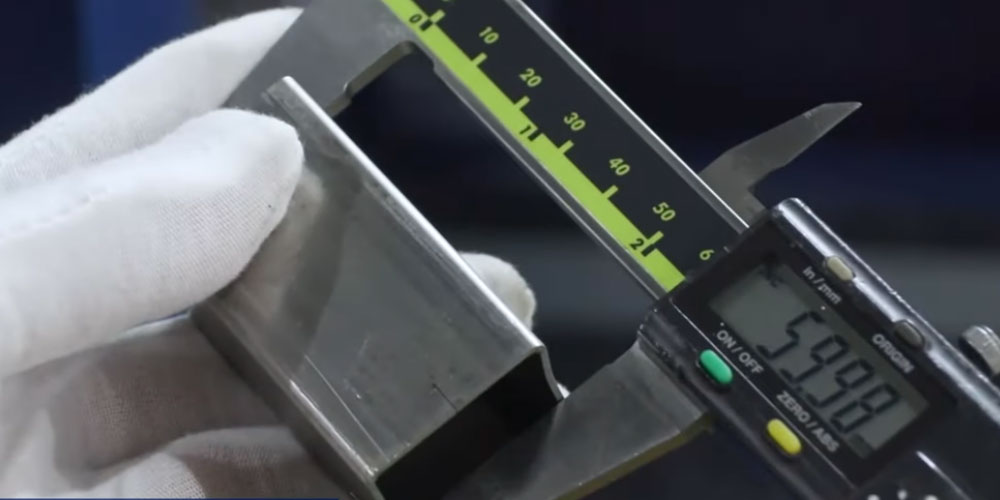
by Eric St. James
Published at 2014-03-13
Modern metal fabrication companies are always looking for ways to increase productivity and bring in new business.
Advancements in today’s fabricating equipment and productivity tools, as well as materials and applications, enable fabricators to enjoy many more options and opportunities than in the past and this is particulalry relevant in waterjet and laser-cutting.
Waterjet and laser cutting are the most popular cutting processes utilized by metal fabricators today. Determining which one is the best for your business largely depends on your cutting requirements and the desired end result.
Factors to considerWaterjets can easily process non-metallic materials and can effectively cut plastics and rubber materials without releasing toxic gases.
Traditionally, tapering of the cut edge has been cited as a disadvantage by metal fabricators using a waterjet system. However, new machine features like Waterjet USA’s Taper Control Technology can relieve this issue.
Another problem facing waterjet users is the cost of garnet recovery. Now automated garnet recovery systems result in lower maintenance costs for machine shops.
Waterjet cutters can effectively handle highly reflective materials such as brass and copper which can be particularly difficult for lasers to cut unless you own a new Fiber Laser.
The versatility that a waterjet machine offers can help niche suppliers branch out of small market segments and appeal to a much broader customer base.
Modern laser-cutters can quickly and easily switch from one metal to the next with little downtime thanks to built-in cut conditions found in onboard databases within the CNC control.
Lasers can process materials other than metals but on plastics and rubbers, hazardous chemical byproducts can be released, so lasers may not be the best choice if these are materials your shop is required to cut.
Laser cutting can provide short lead times and excellent material usage making it a fast and economical method of sheet metal cutting. It can also be a good tool for both pre-production samples and small to moderate sized production batches.
Cutting MaterialsBoth waterjet and laser equipment can be utilized when cutting many different types of materials. For cutting metals under 1” in thickness, lasers are your best bet. When cutting material thicknesses in excess of 1” waterjets will get the job done. Waterjets can also easily cut virtually any type of material. When making a decision of which machine to use, It basically boils down to what material your shop is being required to cut.
stainless steel | carbon steel | tool steels | titanium | aluminium | brass |
wood | Kevlar | plastics | rubber | foams | ceramics |
marble | granite | glass | copper | armour plate | Hastelloy |
stainless steels | carbon steels | steel alloys | aluminum |
Hastelloy | wood | plastics | plexiglass |
also can be utilized in specialty jobs e.g. etching and engraving |
Overall Pros and Cons
Choose the right cutting machine for your operation based on your company’s needs and budget.
Typical pricing:
Waterjet cutter - 5 foot x 10ft. 3 axis machine – $150,000 – $250,000
Laser cutter - 5 foot x 10ft. 4000 watt machine - starting at approx. $500,000
Whether you purchase a waterjet or a laser, the new machine technologies available today enable manufacturers to offer more varied services to their customers than ever before. Utilizing the latest cutting equipment boosts productivity and helps companies increase business.
© 2023 Paramount Machinery Inc. All rights reserved.