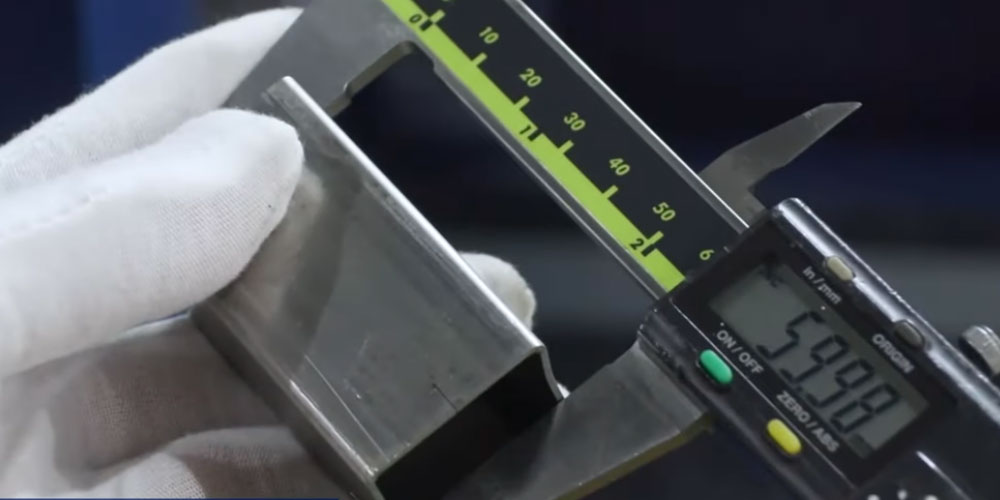
by Eric St. James
Published at 2020-07-10
Plasma cutting is a popular sheet-metal cutting process that many metal fabricators employ across North America – from large-scale industrial fabrication to small shops. Dating back several decades, the technology has evolved over time with the ability to produce fine quality cuts in a wide variety of materials while maintaining productivity and versatility. This cutting technique can cut through any thick or thin conductive material, including steel, aluminum, brass and copper.
The three fundamental states of matter are solid, liquid and gas. Plasma is the fourth.
These different states of matter are differentiated by the application of energy. When you add more energy (i.e. heat), the state transforms. Let’s explain the concept using ice as an example. When you apply heat, ice (solid) melts to water (liquid). With more heat that water turns to steam (gas). When you add yet more heat, that steam then becomes ionized or electrically conductive (plasma) when the atom loses an electron and becomes positively charged.
A Plasma cutter will use the plasma to transfer energy from a power supply to any conductive material resulting in a clean and fast cutting process.
The main components of Plasma are Power Supply, Arc Starting Console and Plasma Torch. The Power Supply is responsible for maintaining the plasma arc throughout the cut. The Arc Starting Console produces the spark inside the Plasma Torch to create the plasma arc. The Plasma Torch provides proper alignment and cooling of the consumables.
Plasma cutting is a thermal cutting process, using heat to melt the metal. Here’s how it works:
Different Plasma Cutting Systems will vary to some extent, but the basic principles remain the same.
Plasma Cutting Systems
Plasma Cutting is typically grouped in two categories:
Conventional Plasma Cutting: This process uses oxygen, shop air, or nitrogen for cutting. The arc is constricted by the nozzle only and no shielding gas is added. Best used in mechanized applications where the part tolerances are more forgiving.
Hi-definition Plasma Cutting: This process uses oxygen, air, nitrogen, argon/hydrogen, and nitrogen/hydrogen gases for cutting. The torch and consumables are used to further constrict and shape the arc. This system will produce high quality cuts and the angle to these parts is minimal.
Plasma Cutting offers:
Plasma Gas/Shield | Plasma cutting mild steel | Plasma cutting stainless | Plasma cutting aluminum | |
---|---|---|---|---|
Air/Air | Good cut quality/speed. Economical | Good cut quality/speed Economical | Good cut quality/speed Economical | |
Oxygen (O2)/Air | Excellent cut quality/speed. Very little dross | Not recommended | Not recommended | |
Nitrogen (N2)/CO2 | Fair cut quality, some dross. Excellent parts life | Good cut quality Excellent parts life | Excellent cut quality. Excellent parts life | |
Nitrogen (N2)2/Air | Fair cut quality, some dross. Excellent parts life | Good cut quality Excellent parts life | Good cut quality Excellent parts life | |
Nitrogen (N2)/H20 | Fair cut quality, some dross. Excellent parts life | Excellent cut quality. Excellent parts life | Excellent cut quality. Excellent parts life | |
Argon Hydrogen/N2 | Not recommended | Excellent on thick >1/2" | Excellent on thick >1/2" | |
Hypertherm |
Plasma cutting is also cost effective. With capital costs a fraction of the price of fiber lasers, plasma cutters can be a great alternative depending on your needs.
This relatively accessible technology is effective and widely used for a variety of applications. Widespread use includes ship-building, industrial fabrication, and even decorative applications for signage and sculpture.
{{cta('3f32ceac-3de2-4a15-b6b3-627a897fa4c4')}}
© 2023 Paramount Machinery Inc. All rights reserved.