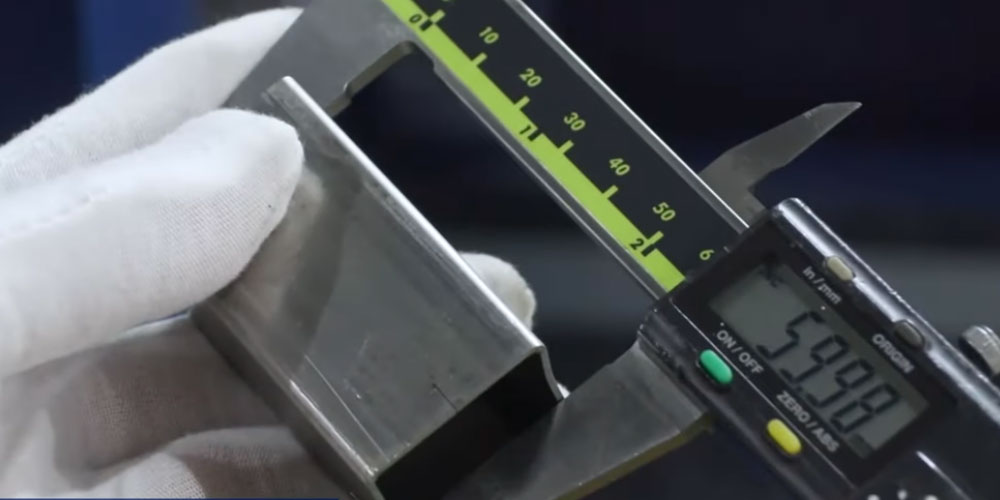
by Eric St. James
Published at 2020-02-26
CO2 lasers have long reigned supreme in the metal fabrication industry. That is until fiber lasers first started gaining traction in 2008 and have been steadily growing in popularity. They’ve also grown in power, with swift innovations driving the early 1kW fiber lasers up to as high as 15kW since they came on the market. Fiber Lasers quickly became the new favourite, gaining market share majority by 2014.
This rapid rise to fame is no mistake. Boasting several key advantages, Fiber Lasers have been replacing CO2 machines in many shops worldwide. Here’s why:
One of the top draws of Fiber Laser systems is the sheer power, efficiency and cut speeds that outrank CO2 lasers, especially for thin materials. When compared against comparable CO2 machines, Fiber Lasers can cut 1mm mild, galvanized or stainless steel up to three times faster. We’re now up to 15kW Fiber Laser from Eagle Fiber Laser, which can cut up to 4 times the number of parts per hour than the 4kW machine. With the technology still evolving, and almost limitless opportunities for power, we expect to see exponentially higher output from these machines in the future.
The best part? That increased cutting speed can convert into dollars. The faster you cut, the deeper your pockets; those extra parts per hour can seriously boost your profits.
Compared to CO2, Fiber Laser cost far less to operate – in fact, they’re up to 50% cheaper to run. CO2 machines need routine upkeep, requiring regular maintenance in the beam path and the resonator. And that’s not cheap. Fiber lasers, on the other hand, have a simpler, more efficient design that leads to minimal maintenance and downtime. Service costs are reduced by approximately 50% and they can run for 50% longer between servicing. Keep on cutting!
Whether you’re an eco-warrior or simply looking to boost your bottom line, fiber lasers are a winner when it comes to energy consumption. Solid state resonators consume less electricity, for the same (or better) output. Overall energy consumption is up to 50% less than comparable CO2 machines. Another way they reduce power consumption? Unlike CO2 machines that must be constantly running due to slow, time-wasting boot-ups, Fiber Lasers hibernate when not in use and can power up immediately.
In addition to the savings on your energy bill, you may be able to take advantage of added incentives or government rebates for adopting power-saving technology. These vary by region, but we encourage you to look into what your province offers or check out saveonenergy.ca/ to see if you qualify for any incentives.
When it comes to any new technology on the market, we can’t forget the “keeping up with the Jones” mentality. We see it with consumer goods, and it trickles in to business in the manufacturing industry as well. Cool factor aside, metal fabricators are finding that upgrading to Fiber Lasers is becoming necessary to stay competitive. As Fiber Lasers become more prevalent, your competitors are going to be reaping the benefits. Whether they start charging less or fulfilling jobs faster, fabricators with more powerful equipment are getting the upper hand.
From top to bottom line, new innovations in Fiber Lasers come with a host of benefits and metal fabricators around the world are taking note. While CO2 is certainly still a player in the industry, Fiber Lasers are starting to outpace them – and with the power, cost-savings and profit opportunities, that’s no surprise. If you’re looking to make the switch now's the time.
{{cta('849fa231-0b41-4ba1-abb3-6a1718e8c43f')}}
© 2023 Paramount Machinery Inc. All rights reserved.