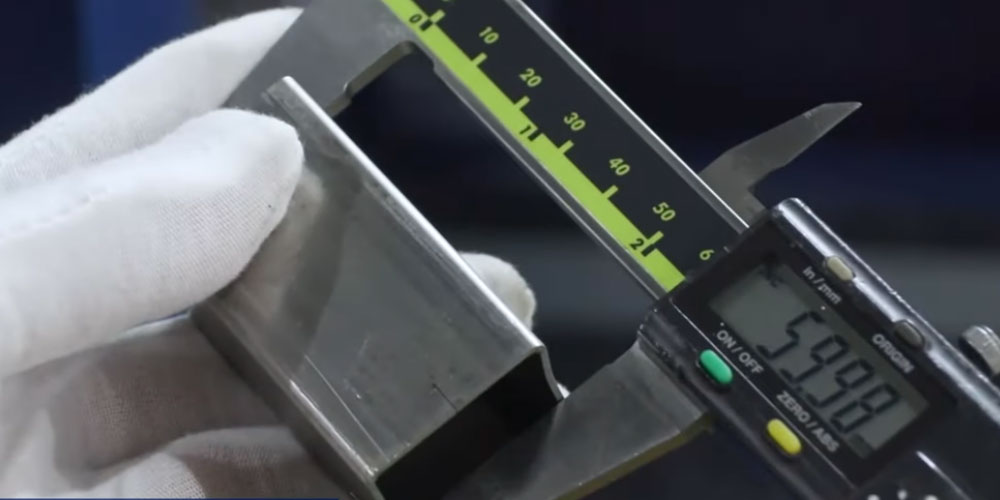
by Eric St. James
Published at 2022-06-28
An assist gas is required with any laser-cutting process. Primarily, assist gas is used to blow molten metal away from the beam kerf, but it also helps protect the lens from molten material splatter thereby improving equipment longevity.
The most common assist gasses in the metal fabrication industry today are nitrogen, oxygen, and compressed air. We often get asked, “how do I know which assist gas to choose?” The answer is usually, “it depends”.
When choosing an assist gas, it really comes down to material type and thickness, application, and desired cut quality.
Oxygen was the top choice in the early years, particularly with CO2 lasers. Oxygen is a reactive gas which is beneficial for cutting materials like thick carbon steel. It is also one of the more cost-effective options as it often runs at a low flow rate and pressure, leading to less consumption and operating costs. Unfortunately, oxygen leaves a black, oxidized edge and speed is limited.
Nitrogen is known for producing high quality edges and became a top choice for many fabricators especially for precision work. It is considered non-reactive or inert, so it doesn’t react with metals during cutting like oxygen does.
Nitrogen is a good option, for materials like aluminum, mild steels and galvanized steels, especially thinner sheets.
When using traditional methods for supply, via a third-party supplier, nitrogen use can get pricey. The gas alone can account for up to 60% of total operating costs. That’s why many shops are turning to on-site nitrogen generation systems. Benefits of these systems include reduced costs, control over gas supply, customization, less waste and elimination of concerns over transportation, storage and handling.
We have been seeing a rise in the popularity of HPAS (High-performance Air Systems or High-performance Compressed Air) due to growth in Fiber laser use.
As Fiber lasers continue to rapidly gain market share, so does the use of High-performance Air Systems/Compressed Air Systems as an assist gas. It’s becoming one of the most popular options due to its cut quality, convenience and cost, and it may even soon outpace nitrogen.
The capabilities of cutting with compressed air have grown with the increase in power of Fiber lasers. Originally, you wouldn’t dream of a 6kW Fiber laser cutting anything thicker than 0.250” with compressed air. Now with higher-powered Fiber lasers, compressed air is being used effectively with metals between ⅜” to ½” thickness. As Fiber laser power increases, we’ll likely see a shift to using High-performance compressed air with even thicker materials.
Compressed air consists mainly of nitrogen along with about 20% oxygen 1% of argon so you can expect cutting results similar to nitrogen. Compressed air is great for producing quality cuts with clean edges, especially for thinner materials like aluminum.
There has been a definitive shift in assist gasses for laser cutting in recent years. As machine technology evolves, so do assist gas choices. Fabricators are looking for options to best fit their needs. While oxygen once had a good share, it couldn’t keep up with edge quality as nitrogen gained popularity. Now that fiber lasers are gaining market share and power, high-performance compressed air is giving nitrogen a run for its money.
At the end of the day, when choosing between assist gasses, it all comes down to the material type and thicknesses you process, your machines and the edge quality you need.
{{cta('601f05f0-3914-4a8f-87e4-902eb851fa8c')}}
© 2023 Paramount Machinery Inc. All rights reserved.